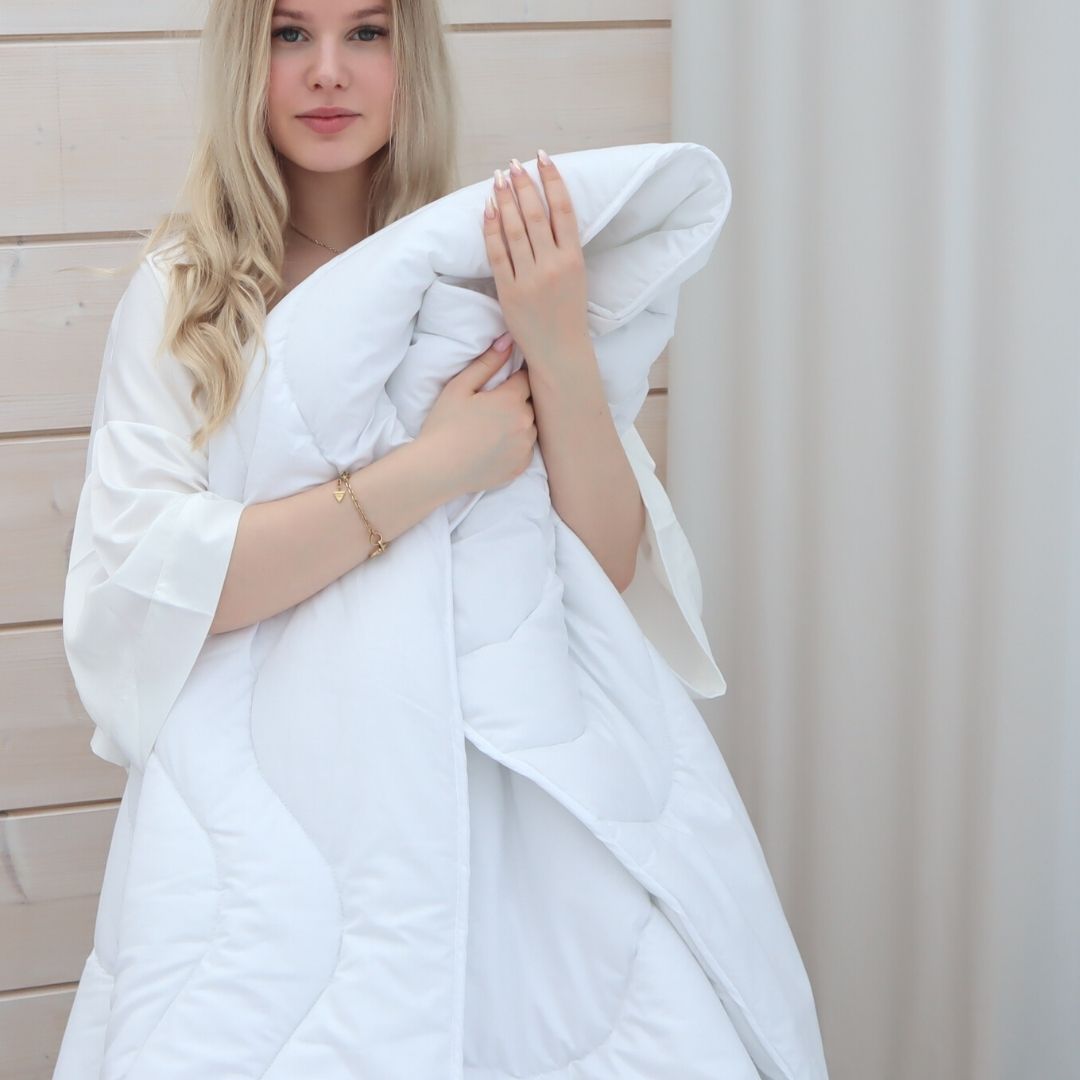
27 Dec Univisio
Univisio is a Finnish company that manufactures bedding textiles – such as blankets, pillows and sheets. The products are manufactured in Finland and the largest customer base consists of various companies and central stores as well as the public sector. Univisio’s products have long used polyester fibre and fabric made from recycled, clean PET bottles, but now the company is also researching the recycling of its own by-products into new products. As a result, Univisio has started cooperating with Rester Oy, which processes textiles into recycled fibres. Univisio will supply Rester with the surplus from its own manufacturing processes, which will be used in the future to manufacture bedding textiles.
“The intention of the entire company is to be able to reduce the impact on the environment and reuse materials,” says Mervi Parkkonen, Univisio’s factory manager.
The use of recycled materials is driven not only by increased consumer interest and appreciation for recycled materials, but also by tightening legislation. Univisio also has an ISO14001 environmental system in place, which supports advanced environmental work. With the environmental system, Univisio must consider the environmental aspects of its products from the outset and also have an open discussion with suppliers in order to meet the required environmental criteria for the materials.
“We have suppliers with whom we have been cooperating for decades, which is a good thing also because they know what we want,” says Tarja Huhtaniemi, Univisio’s purchaser and sales manager.
Univisio’s customers have also expressed interest in products made from recycled materials and wanted the opportunity to recycle end-of-life products. Long and confidential relationships with both suppliers and customers, as well as the company’s small size and agility, have been central to the introduction and development of recycled materials. In addition, their own factory has enabled flexible product development and material testing.
However, working with new materials would not be possible without the commitment of the staff.
“When the entire team is enthusiastic, it’s easier to take things forward,” says Parkkonen.
However, there are challenges in using recycled materials. For instance, some issues in the beginning of the use of recycled polyester were the dark colour of the fibres and the rough feel of the fabric. The quality of recycled materials is often more uneven than virgin, but there have been major improvements in the quality over the years. The challenge is to make a product made from recycled material as high-quality and durable as a product that uses virgin materials. In addition, potentially more expensive materials and a longer manufacturing process must be taken into account and include in the price of the products. However, the price of other materials will also rise in the future, which supports the use of recycled materials.
In regard to the fibre made from Univisio’s own by-products, development work is still in progress, but having worked with recycled polyester, they have both experience and faith in the process. The utilisation of recycled materials is seen by the company as a competitive advantage and, with future legislation, for example, as a necessity.
For companies interested in recycled fibre, Parkkonen and Huhtaniemi hint at the importance of networking and partnerships. Exchanging ideas with other companies and committing to the process are key to success.
“You have to be persistent, it doesn’t happen in an instant,” Huhtaniemi concludes.
In the picture is Univisio’s blanket. Picture: Univisio.